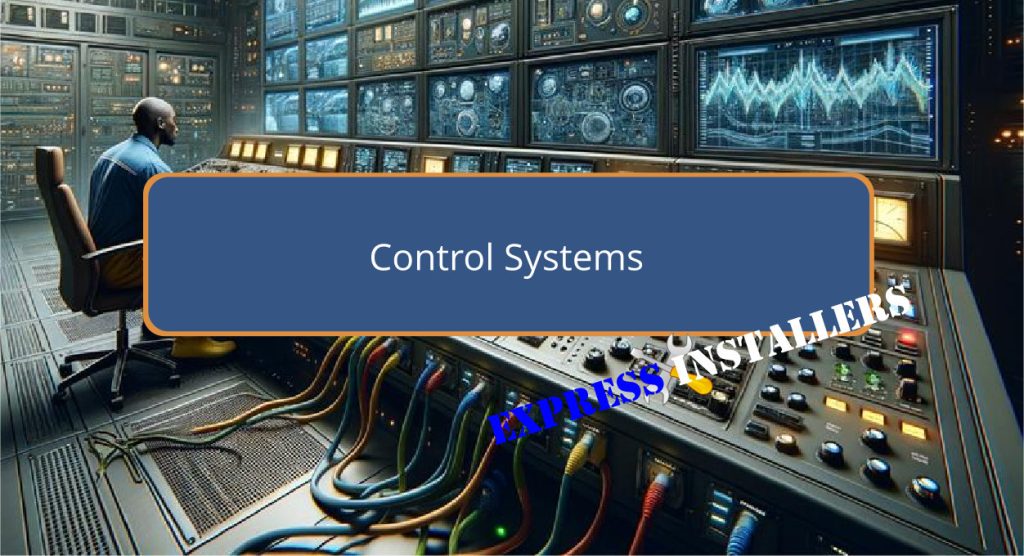
Control systems are engineered frameworks designed to govern the functioning of devices across various industries.
They operate primarily through control loops, categorised into open loop and closed loop systems.
Open loop systems function without feedback, executing fixed instructions irrespective of output changes, while closed loop systems incorporate feedback to dynamically adjust operations based on real-time data.
Essential components such as sensors, controllers, and actuators facilitate the regulation of environmental parameters like temperature and pressure.
These systems are critical in applications ranging from industrial automation to smart farming, ensuring efficiency and stability.
Further exploration reveals the continuous evolution of these systems integrating advanced technologies.
Quick Summary
- Control systems regulate device operations through open loop or closed loop mechanisms.
- Closed loop systems adjust performance using feedback from sensors for dynamic regulation.
- Key components include sensors, controllers, and final control elements for process stability.
- Applications range from industrial automation to power management and smart farming.
- Future trends include AI integration, IoT connectivity, and predictive maintenance techniques.
Basics of Control Systems
Control systems, integral to enhancing production and safety across various industries, utilise control loops to regulate device operations efficiently.
Understanding the fundamentals of these systems is essential for troubleshooting issues that may arise during operation.
Effective maintenance practices are essential to guarantee the longevity and peak performance of control systems.
Regular checks and balances, aligned with industry best practices, prevent potential failures and minimise downtime.
Personnel training is important, empowering operators with the knowledge to identify and rectify faults swiftly.
Systematic documentation of maintenance procedures and outcomes also facilitates continual improvement in system management.
Therefore, a strategic approach to maintenance and troubleshooting not only sustains but also enhances system efficiency and reliability.
Types of Control Systems
Various classifications of control systems exist, primarily distinguished as open loop (non-feedback) and closed loop (feedback) systems.
Open loop systems operate without monitoring or adjusting based on the output signals, which may lead to inaccuracies in dynamic environments.
Conversely, closed loop systems incorporate feedback mechanisms that continuously adjust the control actions based on sensor data.
This feedback loop is essential for stability analysis, ensuring that the system remains stable under various operating conditions.
Additionally, closed loop systems facilitate robust control, enabling the system to maintain high performance despite disturbances and uncertainties.
This adaptability is particularly valuable in industrial applications, where precision and reliability are paramount.
Such systems exemplify advanced control strategies, blending responsiveness with steadfast control.
Components of Control Systems
In the domain of control systems, critical components such as sensors, controllers, and final control elements interact seamlessly to regulate and stabilise process variables.
Sensor technologies play a pivotal role, detecting fluctuations in parameters like temperature and pressure.
These sensors provide real-time data that is essential for the accurate functioning of the system.
Controller algorithms then process this data, making decisions based on predefined criteria to maintain or alter the state of the system.
This involves complex calculations and logic designed to guarantee excellent performance.
Open Loop Vs Closed Loop
Understanding the distinctions between open loop and closed loop control systems is fundamental to grasping their operational dynamics and applications.
Open loop systems operate without feedback mechanisms, executing predefined instructions irrespective of the output’s variance.
This simplicity, while reducing complexity, limits their adaptability and precision under changing conditions.
In contrast, closed loop systems integrate feedback to continually adjust their performance, enhancing both stability and responsiveness.
This dynamic regulation allows for corrections in real time, maintaining the desired output despite external disturbances.
Consequently, closed loop systems are generally more reliable and accurate, but they also require more intricate and robust design elements to manage the feedback and maintain control process integrity effectively.
Control System Applications
Building on the fundamental differences between open loop and closed loop systems, we now explore specific applications of control systems across various industries.
- Smart Farming: Control systems in agriculture automate irrigation based on real-time soil moisture levels, enhancing resource management and crop yield.
- Industrial Automation: In automotive manufacturing, control systems orchestrate robotic assembly lines, greatly boosting precision and operational efficiency.
- Chemical Production: Essential to chemical plants, these systems meticulously manage temperature, pressure, and flow rates to optimise safety and efficiency.
- Power Management: Power plants utilise control systems to fine-tune power generation, transmission, and distribution, vital for maintaining grid stability and meeting variable demand.
Control Theory Overview
Control theory, a critical component of engineering, focuses on the regulation of dynamic systems to achieve specified outputs through the use of feedback mechanisms.
This overview explores how control theory systematically addresses the stability, performance, and robustness of systems across diverse applications.
The field not only encompasses the analysis and implementation of control mechanisms but also spans both classical and modern techniques applicable to single-input and multiple-input systems.
Essential to sectors like aerospace, robotics, and industrial automation, control theory integrates theoretical rigor with practical application, ensuring that systems operate within desired parameters.
This foundational knowledge sets the stage for exploring the specific designs and configurations of control systems in various technological domains.
Control System Design
In the field of engineering, designing a control system necessitates the careful selection of sensors, controllers, and actuators to meet specified performance criteria.
This process is pivotal in ensuring the system’s stability, responsiveness, and robustness to external disturbances.
The choice of components and their configuration relies heavily on both empirical data and mathematical modelling.
- Sensor Selection: Choosing appropriate sensors to accurately measure system variables critical for feedback.
- Tuning Parameters: Adjusting controller settings to optimise system performance and stability.
- Actuator Design: Tailoring actuators to respond effectively under varying operational conditions.
- Robustness Analysis: Conducting simulations and tests to evaluate system performance against disturbances and uncertainties, ensuring reliability under all conditions.
Modern Control Techniques
Advancements in control system design have led to the development of sophisticated modern control techniques that enhance performance and adaptability.
Model Predictive Control (MPC) exemplifies this evolution by optimising control actions based on future predicted outputs, thereby improving operational efficiency.
Similarly, adaptive control techniques dynamically adjust controller parameters in response to observed changes in system behavior, ensuring consistent performance despite external or internal disturbances.
These methodologies are underpinned by robust control theory, which guarantees system stability across a variety of unpredictable conditions, and model identification processes that provide precise representations for effective control strategy formulation.
Collectively, these advanced techniques represent a significant leap forward in the field of control systems.
Challenges in Control Systems
Despite the progress in modern control techniques, practitioners still confront significant challenges such as system complexity, nonlinear behaviour, and environmental uncertainties.
These hurdles are compounded by several specific issues:
- Modelling Uncertainties: Inaccurate models can lead to poor performance and instability, especially in systems with complex dynamics and interactions.
- Adaptive Strategies: Developing strategies that can dynamically adjust to changing conditions and system disturbances is essential.
- Real-time Constraints: Ensuring timely response within very tight deadlines is vital for maintaining system stability and performance.
- Integration of Subsystems: Coordinating multiple components with varying dynamics and specifications requires sophisticated control approaches to guarantee seamless operation.
These challenges emphasise the need for continual development in control methodologies to enhance system reliability and efficiency.
Future Trends in Control Systems
In addition to the integration of artificial intelligence and machine learning in control systems, emerging trends also focus on IoT connectivity.
This combination enables the development of highly efficient, interconnected systems capable of sophisticated data exchange and analysis.
Furthermore, the advancement of cyber-physical systems allows for real-time monitoring and control in complex industrial environments.
This progression is also supported by the implementation of cloud-based solutions, which provide remote access, improved scalability, and robust data storage capabilities.
Additionally, the adoption of predictive maintenance within these frameworks aims to optimise system performance and minimise downtime, ensuring more reliable and sustainable operations across various sectors.
Frequently Asked Questions
What Are the 4 Types of Control Systems?
The four primary classifications include open loop, closed loop, feedforward, and feedback systems, each enhancing system stability through distinct feedback mechanisms and proactive adjustments, critical for precision and efficiency in various operational environments.
What Is Meant by Control System?
A control system orchestrates and manages processes to achieve desired outputs, emphasising feedback importance for adjustments and promoting system stability, ensuring consistent performance across various applications from industrial automation to everyday electronic devices.
What Are the Three Control Systems?
The three primary control strategies enhancing system effectiveness include open loop, where no feedback is used; closed loop, utilising feedback to refine operations; and feedforward, pre-emptively adjusting to disturbances.
Which Is an Example of a Control System?
An example of a system that exemplifies biological feedback and automotive stabilisation is the anti-lock braking system (ABS), which prevents skidding and maintains vehicle control during abrupt braking scenarios.
Conclusion
To sum up, control systems play a crucial role in various applications, ranging from simple household devices to complex industrial machinery.
The progression from basic mechanisms to advanced, computer-integrated configurations demonstrates significant technological advancement.
Despite challenges such as complexity and integration difficulties, ongoing innovations hold the promise of improved precision, adaptability, and efficiency.
Future trends are likely to involve increased automation, AI integration, and cyber-physical systems, indicating the direction towards even more sophisticated and interconnected control environments.